FAQ
Common Questions
What are the Benefits of MTP?
Heterogeneous Integration
-
- Less Waste
- Minimal packaging
- Reduced Heat
- Higher efficiency
- Smaller footprint
- High Throughput
- Faster Time to Market
- Printable on silicon, glass, ceramics, paper, and other semiconductor materials.
- Applications for Photonics, MedTech, IoT and Communications
About the Technology
What is Micro-Transfer Printing? (MTP)
Micro Transfer Printing is a proven process for combining tiny, non-native components on a single substrate. Please see the following examples for further details.
Flexible and Scalable Heterogeneous Integration of GaN HEMTs on Si-CMOS by Micro-Transfer-Printing: The heterogeneous integration of GaN-based high electron mobility transistors (HEMTs) together with silicon CMOS by micro-Transfer-Printing could be a key technology for this. It enables the integration of highly integrated mature CMOS logic functionality with fast GaN HEMT output drivers with very low on-state and switching losses.
A high concentration photovoltaic module utilizing micro-transfer printing and surface mount technology: We describe a high concentration photovoltaic (CPV) module utilizing micro-transfer printed (μ-TP) dual-junction GalnP/GaAs solar cells and an ELO (Epitaxial Lift-Off) process used to fabricate very small cells (<;0.5 mm2) using 1stuse and reused GaAs substrates. The benefits of this technology include high efficiency, simple distributed heat transfer at high concentration ratios, and short optical paths. Source.
Heterogeneous integration of microscale semiconductor devices using elastomer stamps: In micro-transfer-printing an engineered elastomer stamp coupled to a precision motion controller is utilized to pick-up and transfer arrays of microscale devices. A wide range of materials and devices have been micro-transfer-printed, including; Silicon integrated circuits, Gallium Arsenide LEDs, Gallium Arsenide solar cells, Gallium Arsenide lasers and Gallium Nitride LEDs. Devices compatible with micro-transfer-printing are very thin (< 10 microns) and small (< 100um lateral dimensions) and are ideally suited for making flexible device formats and are also well-suited for wafer-level heterogeneous integration. Source.
How does heterogeneous integration work?
Heterogeneous integration is a precise methodology that enables tiny, non-native components to be aligned on single substrate, increasing functionality, improving efficiency and expediting time to market. Here are a few examples.
Heterogeneous Compound Semiconductor Integration: Micro-transfer printing (μTP) provides fast and precise assembly of micro-components from a variety of different source materials onto non-native target substrates such as glass, plastic, ceramic, and silicon. Retrievable micro-components are picked up by an elastomer stamp and printed onto the target substrate with yields exceeding 99.9%. Devices incorporating GaN, GaAs, InP, and other compound semiconductor materials are successfully integrated onto silicon and glass with fine precision to make highly integrated compound semiconductor micro-systems.
Transfer printing of nanomaterials and microstructures using a wire bonder: Scalable and cost-efficient transfer of nanomaterials and microstructures from their original fabrication substrate to a new host substrate is a key challenge for realizing heterogeneously integrated functional systems, such as sensors, photonics, and electronics. Here we demonstrate a high-throughput and versatile integration method utilizing conventional wire bonding tools to transfer-print carbon nanotubes (CNTs) and silicon microstructures. Standard ball stitch wire bonding cycles were used as scalable and high-speed pick-and-place operations to realize the material transfer. Our experimental results demonstrated successful transfer printing of single-walled CNTs (100 m-diameter patches) from their growth substrate to polydimethylsiloxane, parylene, or Au/parylene electrode substrates, and realization of field emission cathodes made of CNTs on a silicon substrate. Source.
Does MTP print chips for biomedical devices?
Some great innovations in the medical field have already taken place – and many more to come. From DNA arrays to labs on a chip, the potential for the healthcare industry seems limitless. Here are a few examples.
Printing of temperature and humidity sensors on flexible substrates for biomedical applications: Printed electronics have become of great interest over the last few years, mainly because of the benefits it would bring. These advantages, a reduction of fabrication cost, an easy possibility to print on flexible substrates, and the versatility can be easily applied to wearable and medical domains. Here we present results of a flexible hybrid-printed temperature and humidity sensor with printed electrodes using thermal transfer technic with a donor ribbon. Those electrodes are interdigitated and covered with graphene oxide. The innovative thermal transfer printing technology allows the deposition of various types of conductors in a solid-state. It then contributes to have a resistivity nearer to the bulk as compared to other printing technics. A drop-casting layer of graphene oxide acts as the temperature and humidity sensing material. His electrical properties change as a function of the conditions. These kinds of printed sensors could be easily integrated into smart bandages. Some of the most innovative applications of micro-transfer printing are in MedTech industry. Source
Transfer Printing of Electronic Functions on Arbitrary Complex Surfaces: Transfer printing of electronic functions on arbitrary surfaces is essential for next-generation applications of skin-attachable electronics, wearable sensors, and implantable/medical devices. For transfer printing of electronic functions on multidimensional surfaces, such as curved regions of the skin and different objects, various strategies have been devised based on the materials and structural design of electronic components and transfer stamps, such as ultrathin membranes or in-plane structures of electronic components, soft interfacial glues or adhesives between devices and surfaces, and smart transfer adhesives with bioinspired micro/nanostructures. These techniques enable high conformity of adhesion, mechanical robustness, and high compliance of electronic devices on arbitrary surfaces under mechanical deformation.
Micro Light-Emitting Diodes for Display and Flexible Biomedical Applications: Inorganic-based micro light-emitting diodes (µLEDs) have witnessed significant improvements in terms of display and biomedical applications, which can shift the paradigm of future optoelectronic systems. In particular, µLED displays are on the verge of becoming the next big interface platform for visual communications, expanding to various internet of things and wearable/bioapplications. Novel µLED concepts need to be upgraded to be able to satisfy their potential optoelectric applications, such as virtual reality, smart watches, and medical sensors for individual computing in this hyperconnected society. Here, representative progresses in the field of flexible µLEDs are reviewed with regard to device structures, massive µLED transfers, methods for performance enhancement, and applications.
Is the technology licensed?
Yes. Clients secure a license for the technology before bringing the final product to market.
About the Process
Where do we start?
We begin with a meeting to understand your requirements, explain the technology and create an agreed upon Scope of Work, deliverables and outcomes. NDAs are signed before proprietary information is shared.
The first step is establishing a sound design. We provide design support for a client’s development team, collaborating on the effort.
The next step is to support the development of a prototype. Again, we provide assistance to clients who choose to do the development themselves and, on some occasions, build the prototype in house.
Can you provide printing services?
Yes. We have micro-transfer printing cleanroom facilities at the Tyndall National Institute in Cork, Ireland, and at our Development Center in Durham, North Carolina. We print the final x-chip in either location.
Do you consult with customers?
Lastly, we consult with MedTech companies to assist with
medical device submissions. Getting approval from the FDA and EMA is a time-consuming and costly process.
Do you offer technology transfer?
We offer a range of support services from consultation to full process start-up. We also maintain an extensive library of technology transfer documentation detailing each process step.
Micro-Transfer Printing takes place in a cleanroom environment to maintain the integrity of the process. We have labs for printing at the Tyndall National Institute in Cork Ireland and at Micross in RTP, North Carolina.
Need Something Else?
If you need answers to other questions, please don’t hesitate to contact us at info@x-celerprint.com.
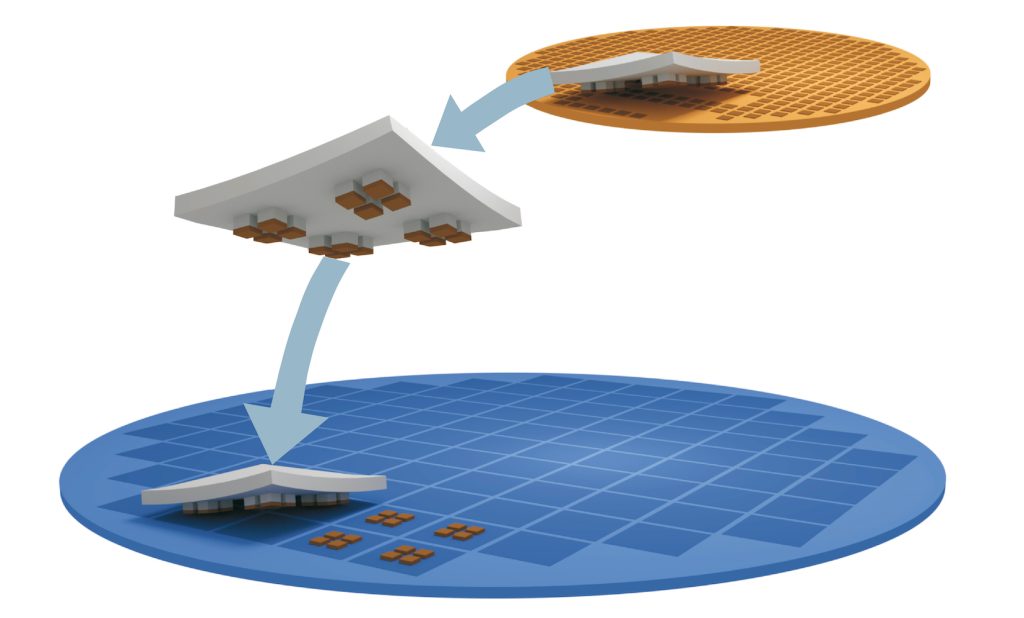
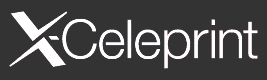
X-Celeprint is an international leader in micro-transfer printing. Our headquarters are at the Tyndall National Institute in Cork, Ireland. We also have a Development Center in Research Triangle Park, NC. We serve customers in North America, Europe, and the Asia Pacific. We provide our clients with design support, prototyping, printing, licensing, and tech transfer for commercialization.